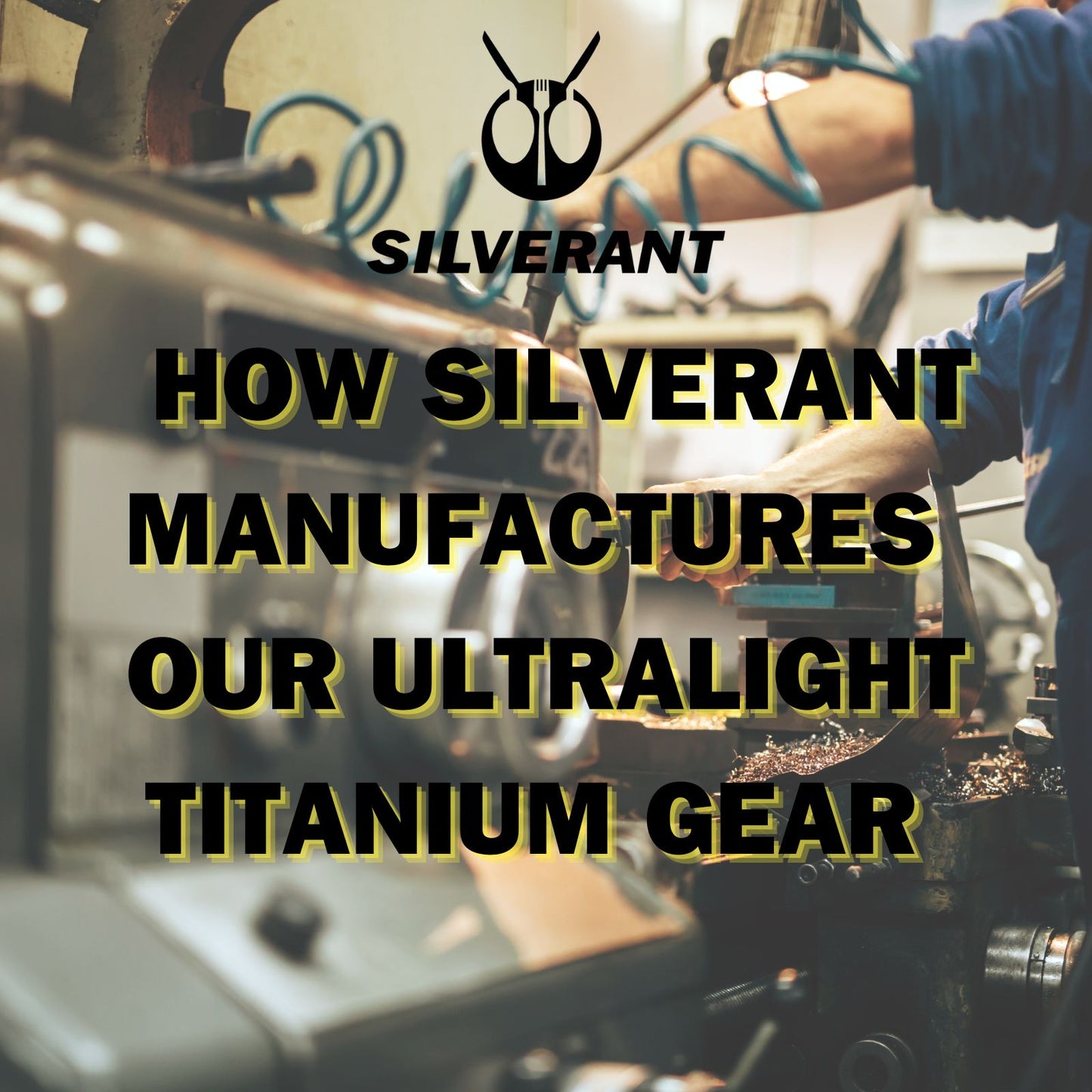
1. Sourcing
2. Cutting
3. Pressing
4. Welding
5. Buffing/Sandblasting
6. Cleaning
7. Logo Engraving
8. Packaging
Before SilverAnt was established in 2018, we were already a titanium manufacturing specialist. As one of the largest titanium outdoor producers worldwide, we had built up a huge knowledge. It is this strength that lead to SilverAnt's founding.
As a company, we are proud to own our own ISO:9001-2015-certified manufacturing facility. To achieve international recognition for manufacturing is a great achievement. Our factory has held this certification since 2011, with the factory beginning operation way back in 2003. It is why SilverAnt is proud to offer a lifetime guarantee for every customer order. We stand behind our ethos of ultralight titanium gear built for a lifetime of adventures.
So without further delay let's embark on our 8-step manufacturing process.
Sourcing

At SilverAnt we create all our products from sheets of titanium. These sheets of titanium come from our supplier based in Sichuan Province, Western China. In Sichuan province, there are large deposits of pure titanium. China holds the largest reserves of titanium minerals worldwide. The majority of this is in the mineral Ilmenite.
In fact, Sichuan province now produces a large percentage of the world's entire titanium supply. Companies such as Boeing and Airbus source titanium here for producing airplanes.
Cutting
When the sheets of titanium arrive at our factory they need hoisting with a crane to our storage area. The sheets of titanium we buy either as large flat sheets or rolls of titanium. The rolls of titanium are particularly useful as less manpower or machinery is needed in their movement across the factory.
With every product we make there are multiple steps in their production. By this I mean we often need to make molds for two or three titanium shapes which then make the complete product. Each product we make has an exact size specification we cut into the titanium sheet. Every product component has its own set of specific molds for cutting. These molds are for the precise replicable cutting of each component step. To scale production we make many copies of the mold to increase speed.
After cutting the specific shapes for each product phase we then recycle any remaining titanium. One of the key components of the cutting process is to reduce waste. This serves two purposes. First titanium is an expensive commodity. Second to have high waste from cutting increases operation costs but more so it is not eco-friendly.
The entire aim of the cutting manufacturing phase is to have the exact shape for the next step of manufacturing. With many copies of the exact shape, we need to then press, roll or fold.
Pressing
When pressing the titanium sheets, SilverAnt uses press machines. In our factory, we have many press machines and these are all located on the ground floor. The press machines are extremely heavy as they operate using weight to create the exact shape for each product.
Press machines and every manufacturing facility that uses them worldwide rely on them for easy customization. By customize I mean you can attach many different product molds. This allows SilverAnt to use one machine rather than many specialized machines. Each new product we create will then only need the initial investment in the mold for production.
For our water bottles, we take the cut rectangular titanium sheet and place it in a rolling machine giving the cylindrical shape. With our hip flask collection, we use a rolling and folding machine.
With our titanium cutlery/flatware we use a cutting machine with a mold for each piece of cutlery.
For all SilverAnt cups as well as for the camping cookware pots and pans we use a press machine.
SilverAnt takes the pre-cut circles of various dimensions and then aligns them in the pressing machine before activating the press. For example, the 400ml, 500ml, and 600ml cups all have slightly different circle sizes. With the specific press mold used for each product, we get the exact size needed.
To ensure that the surface of the titanium isn't affected by the press machine's weight and the friction caused by pressing, a blue film is used on the surface of the titanium. We also use a lubricant on the surface of the film during pressing too.
After pressing with the specific product mold we need to further cut any excess titanium. Once again we use a custom mold for each product to do this. All excess titanium cuttings are then recycled.
Welding
After each of the product components have been pressed, cut, and rolled, SilverAnt then needs to assemble these pieces together. To do this we use precise laser welding technology. We pair the experience of our technicians with laser technology to weld all product components together.
To operate we use computer-aided welding programs with a preset operation frame. This is set by our technicians. Once this is preprogrammed into the computer it is replicable and efficient. During laser welding, our technician monitors the progress while checking quality.
When welding it is important to ensure a sturdy platform. To ensure this each welding step has again its own mold. We typically use stainless steel for each of our molds because of its durability.
To give an example for laser welding a water bottle drinking area welded to the main body takes between 120-180 seconds. The larger the water bottle body the bigger the welding surface. With each weld complete it is checked by our technicians for any imperfections.
Buffing and Sandblasting
With the laser welding complete all products move onto the buffing and sandblasting stage of production. Like a bicycle with the classic industry standard fish scale welding pattern. Every weld should be buffed to create a smooth surface.
Once every product has been buffed we then move on to sandblasting. Sandblasting is the titanium industry standard and gives an even finish for every SilverAnt product. We sandblast because titanium gets dirty during the cutting, pressing, and welding phases. It has residue from welding and micro-particles from cutting. Also, titanium naturally has areas of discoloration and the abrasive sandblasting removes this.
In a previous article, I explained the difference between sandblasting and crystallization. Sandblasting is an abrasive finish and not a coating or lining.
In an enclosed machine we use thousands of abrasive micro-particles and spray the titanium product with an item like an air gun. This produces the classic titanium finish. If the titanium were coated after using once or twice on a camp stove or fire the lining/coating would peel.
After sandblasting every product undergoes a deep clean which is broken into two phases.
Cleaning
With the previous production phases complete a deep clean is needed.
From the previous stages of production, there can be oil lubricant residue from machines, micro-particles from sandblasting, and other particles from welding. To completely remove these we first put every product in an ultrasonic water bath. The water temperature is 100°c and with the seismic movement, every product gets deep cleaned.
At each stage of production, our technicians perform quality control checks. Nevertheless, prior to cleaning and ultimately assembling products a final check is done. Any imperfections and the product returns to the specific phase of production.
After the 100°c water bath, the products are placed in a cold water bath. This is to rinse every product. Once each product goes through these two steps the product is dried with an air gun and cloth, before being left to completely dry. When each product is dried and aired product assembly takes place.
Product assembly is adding lids to water bottles and cups, carabiners to cutlery sets, and braided para-cord to kettle handles.
Logo Engraving
With each product assembled, we then move on to the penultimate phase of manufacturing. We need to add the SilverAnt logo to each product. To do this we use laser engraving with computer-aided design.
Every product SilverAnt makes has a preloaded design and logo location. For each new product, we set and experiment with the best location and then program it into the computer. The technician with the aid of metal blocks secures the product placement before placing enter on the computer.
Every logo laser engraving takes between 30-120 seconds depending on the logo size and placement. For some titanium products, we add the capacity with the logo engraving. But for items like cutlery, they just have the standard SilverAnt logo.
Packaging
The last and final step of the SilverAnt manufacturing process is to pack each product. In this stage, we will put product items together. Hip flasks will be packed with titanium funnels, coffee cups with straws, thermal sleeves with water bottles, and so on.
Each product is placed inside a plastic bag before closing and putting it in the correct size cardboard box. For cookware, cutlery, cups, and stoves each product gets a handy drawstring case too.
Once packed SilverAnt stores every product in our warehouse ready for worldwide shipping.
SilverAnt is in a unique position because of our manufacturing facility. It enables us to control quality ensuring the best titanium gear for our customers. When you buy from us receive a lifetime warranty as standard!
Thanks for reading. If you liked this article make sure to check out our accompanying manufacturing YouTube series.